The experimental work of ISEE in several examples
The experimental work of the Institute for Systemic Economic Engineering (ISEE) in defining the capabilities of the Business Digital Twin (BDT) system and the Business Model Ontology (BMO) is a multi-annual cognitive accumulation process. This process has been continually aligned with the creative endeavors and research work of the organization. Unlike traditional consultancy practices or software integrations, our experiments have consistently yielded exceptionally high returns on investment (ROI). The implementations have proven sustainable and demonstrated the significant economic impact of BMO and BDT on business enterprises and their economic management.
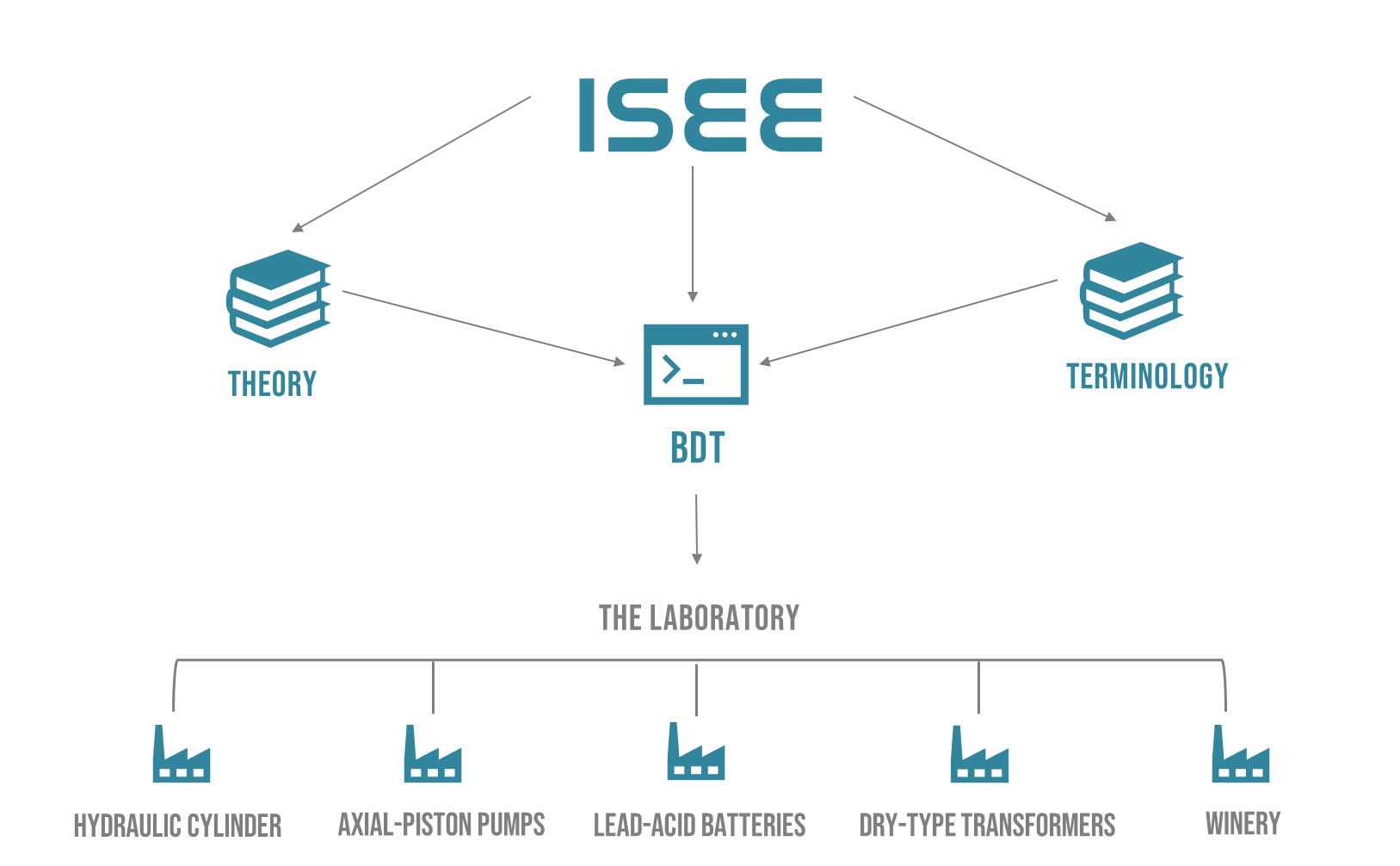
Applied Laboratory Base
ISEE operates through a unique applied laboratory base, which serves as the experimental ground for testing and refining the BDT system and BMO framework. This base includes a variety of business enterprises where real-world applications of our theories and systems are implemented and evaluated. The outcomes from these experiments not only validate the theoretical constructs of BMO and BDT but also highlight their practical benefits in enhancing operational efficiency and economic performance across different industries.
The BDT system as a bearer of knowledge for:
The BDT system as a bearer of knowledge for:
Implementation site: Unitraf JSC, Bulgaria.
Overview:
In 2021, Unitraf JSC, a manufacturer of transformers, reactors, machined parts, and components, embarked on a transformative, organizational reengineering journey by implementing the Business Model Ontology (BMO) within their management practices. This initiative aimed to completely remodel the organizational culture in line with BMO theory, aiming to achieve significant advancements across the enterprise.
The Experiment:
The implementation was initiated by the owners of Unitraf JSC within their dry-type electrical transformer and metalworking enterprise comprising 50 employees. A new management team, appointed without prior experience in enterprise management, led the transformation. The focus was on adopting the BMO principles as the enterprise’s organizational culture with the aim of enhancing the organizational structure, optimizing processes, and fostering a culture of continuous and sustainable improvement.
Outcome:
The results of the BMO implementation were as follows:
- Profit Surge: The enterprise saw a 357% surge in profit, underscoring the financial success driven by the new management practices.
- Revenue Growth: Within one year, Unitraf JSC experienced a 50% increase in revenue.
- Value Addition: There was a significant 127% increase in added value, reflecting enhanced operational efficiency and product quality over the three divisions of the enterprise – transformers, manufacturing, electronics.
- Product Diversification: The company ventured into electronic equipment manufacturing, including UPS devices and sales of Solar Hybrid Inverter solutions, further diversifying its product portfolio.
- Employee Compensation: The average salary of employees increased by 50%, showcasing the positive impact on workforce motivation and retention.
- Infrastructure Expansion: A new manufacturing hall was constructed, and the shop floors of both the transformer manufacturing and metalworking operations were expanded.
The implementation of BMO at Unitraf JSC demonstrated the transformative impact of strategic, theory-based organizational management on SMEs. By remodeling the organizational culture and optimizing management practices, Unitraf JSC not only achieved substantial financial and operational improvements but also laid the foundation for sustained growth and innovation in the manufacturing sector. This case exemplifies how SMEs can leverage BMO to achieve industrial excellence and competitive advantage in their respective markets.
Implementation site: Unitraf JSC, Bulgaria.
Overview:
Hydraulic Elements and Systems PLC (HES) is the primary laboratory-enterprise within the Applied Research Base of ISEE. Before the democratic changes of late 1989, HES operated with over 2,500 employees across four manufacturing sites. At that time, the company held over 20% of the global market for hydraulic cylinders used in electric and motor forklifts. However, by March 1997, HES was near bankruptcy, with only around 1,000 employees and an average salary of less than $10 a month. The technical environment was in a deplorable state.
The Experiment:
In March 1997, Peter Bachvarov, a co-author of the Business Model Ontology (BMO), was elected CEO at HES. This marked the beginning of a transformative journey for the company, focusing on implementing the BMO and developing the Business Digital Twin software.
- 1997-2001: Initial Phase
Recruitment and Training: HES hired 12 young machine engineers with minimal professional experience in 1997. By mid-1998, these engineers were introduced to the initial form of the holistic BMO.
Development of BDT: An initial variant of the 1st version of ISEE’s Business Digital Twin was provided to these engineers, enabling digitalization of engineering developments to manage sales, production, and supply systems. The first version of the BDT was completed by the end of 2001.
- 2002-2003: First Campaign for Large-Scale Industrial Reengineering
Restructuring and Relocation: Over 80% of all workplaces were restructured and relocated within 15 months, managed by those young engineers using the Business Digital Twin software.
Focus on Engineering Developments: The engineering developments included labor norms, material limits, and “engineering organizational cost analyses” of products, all embedded in the Business Digital Twin.
- 2010-2011: Second Campaign for Large-Scale Industrial Reengineering
Economic Crisis Response: Following the global economic crisis, a second reengineering campaign was launched, utilizing the 3rd version of the BDT system.
Continued Improvement: This campaign saw over 70% of workplaces restructured and relocated, resulting in a more than twofold increase in production volume and diversity.
Outcome:
The results of the two campaigns demonstrated a profound transformation at HES.
Technical Environment Transformation:
The state of the technical environment improved significantly from 1997 to 2011, with modernized equipment and processes. Before the implementation of BMO, the technical environment was outdated and inefficient, but by 2011, it had been transformed into a state-of-the-art facility. This included upgraded machinery and streamlined production lines, which greatly enhanced operational efficiency.
Economic Growth:
Sales increased substantially over the twenty-year period, despite the global economic crisis of 2008/2009. The holistic ERP system enabled better resource management, cost control, and market responsiveness, which resulted in a steady increase in revenue. Even during economic downturns, HES managed to maintain growth by optimizing its production processes and expanding its market reach.
Batch Size Reduction:
The ability to engineer and manufacture products in small batches improved dramatically, enhancing flexibility and efficiency. Initially, HES operated with large batch sizes, which limited its ability to respond to market changes. By implementing the holistic ERP system, the company was able to reduce batch sizes, allowing for more customized production runs and quicker turnaround times.
New Product Implementation:
The capability to introduce new products saw significant growth, from no new product engineering developments in 1997 to a robust system by 2011. The holistic BMO framework facilitated innovation by integrating product development with production and supply chain management. This seamless integration allowed HES to rapidly develop and launch new products, meeting evolving customer demands.
Organizational Shift:
The role of engineers evolved from servicing in 1997 to central management by 2003, reflecting a shift towards a knowledge-driven organization. The transformation involved not only technological advancements but also a cultural shift within the organization. Engineers became central to the decision-making process, leveraging their expertise to drive strategic initiatives and continuous improvement
The transformative journey of HES, powered by the holistic BMO and a holistic ERP system, highlights substantial improvements in the technical environment, economic performance, and organizational structure. This case study underscores the efficacy of BMO in driving large-scale industrial reengineering and achieving sustainable growth. The success of HES demonstrates that with the right strategic approach and technological integration, even enterprises on the brink of failure can achieve remarkable turnaround and long-term prosperity
Implementation site: Hydraulic Elements and Systems PLC, Yambol, Bulgaria.
Overview:
ISEE has executed numerous industrial reengineering campaigns, with two major initiatives reshaping over 500 workplaces. The first of these large-scale efforts demonstrated the transformative power of the second version of the Business Digital Twin (BDT) system.
First Campaign: 2002-2003
The Experiment:
The initial large-scale reengineering campaign was conducted over approximately 15 months, between 2002 and 2003, utilizing the second version of the BDT system. During this period, over 80% of all workplaces were restructured and relocated. Remarkably, the project was managed by several young engineers, each with less than three years of professional experience but highly proficient in using the BDT system for modeling technological environments and industrial processes.
Outcome:
The campaign was executed swiftly and efficiently without any interruption to industrial processes. In fact, production volume and diversity increased during the reengineering process. The success of this campaign highlighted the effectiveness of the second version of the BDT system in managing and executing large-scale industrial transformations with minimal disruption.
Second Campaign: 2010-2011
The Experiment:
Following the global economic crisis, ISEE embarked on a second large-scale industrial reengineering campaign from the spring of 2010 to the summer of 2011, utilizing the third version of the BDT system. During this period, more than 70% of all workplaces were restructured and relocated. This initiative was undertaken amidst challenging economic conditions, underscoring the resilience and adaptability of the BDT system.
Outcome:
Despite the economic downturn, the reengineering campaign proceeded without delays or suspension of industrial activities. Production not only continued but accelerated, with a more than twofold increase in both volume and nomenclature. The campaign’s success was unprecedented, with ISEE’s studies indicating no comparable industrial reengineering effort in terms of investment efficiency and performance, achieved largely due to the advanced capabilities of the third version of the BDT system.
Conclusion:
These two campaigns collectively demonstrate the BDT system’s unparalleled effectiveness in facilitating large-scale industrial reengineering, even under challenging circumstances. The evolution from the second to the third version of the BDT system showcased significant advancements in technology and methodology, enabling remarkable improvements in productivity and operational efficiency.
Implementation site: Hydraulic Elements and Systems PLC, Yambol, Bulgaria.
Overview:
In 2005, ISEE embarked on a project to assess the capabilities of the Business Digital Twin (BDT) software as a system for quality management and as an enabler for a seamless ISO 9001:2000 certification process.
The Experiment:
To thoroughly evaluate the BDT software, ISEE collaborated with two globally renowned certification bodies – Lloyd’s Register and TÜV Rheinland. The project team from ISEE included one engineer proficient in the BDT software and an assistant. The consultants from Lloyd’s Register and TÜV Rheinland initially anticipated that implementing the necessary documents for quality management procedures would take several months, typically around 4 to 6 months, followed by an extended period for the actual certification audit, which usually takes an additional 3 to 6 months. Therefore, they expected the total process to take between 7 to 12 months.
However, upon familiarizing themselves with the BDT software, the consultants discovered that all necessary forms and information were already integrated into the system. The only task remaining was to format the information provided by the Business Digital Twin according to the standards recognized by the certification bodies.
Outcome:
Remarkably, by mid-December 2005, less than two months after the project commenced, Lloyd’s Register and TÜV Rheinland issued the ISO 9001:2000 certification to Hydraulic Elements and Systems PLC. Over the following years, TÜV Rheinland frequently used ISEE’s implementation as a model of “good practices” for other companies seeking ISO 9001:2000 certification, showcasing the effectiveness and efficiency of the BDT software.
Implementation site: Hydraulic Elements and Systems PLC, Yambol, Bulgaria.
Overview:
In 2009, ISEE undertook a project to demonstrate the capabilities of the Business Digital Twin (BDT) software in implementing Single-Minute Exchange of Die (SMED) and lean manufacturing principles.
The Experiment:
Between 2009 and 2010, over the course of 18 months, two engineers with no prior experience in plant design or lean manufacturing theory, but highly proficient in the ISEE Business Digital Twin BDT system and its cognitive platforms, developed and implemented a system for SMED and lean manufacturing. This system was deployed across two technological fields, encompassing a total of approximately 40 digital programming operational places.
Outcome:
The implementation of SMED resulted in a remarkable increase in productivity, with the 40 operational places in question experiencing a 5 to 10-fold productivity improvement. This was achieved with minimal costs. Additionally, a comprehensive personnel training program was developed to ensure the sustainability of these improvements.
In comparison, developing and rolling out such a system on a global scale within a plant owned by a large Western company would typically take around 6 years, requiring significantly greater human and financial resources. This stark contrast highlights the efficiency and effectiveness of the BDT software in facilitating lean manufacturing practices.
Implementation site: Battery plant Tungstone, Ryazan, Russia
Overview:
In 2010, ISEE initiated a groundbreaking project to assess the Business Model Ontology (BMO) as a tool for educating highly effective leaders, diverging from previous experiments by focusing on theoretical foundations rather than direct digital technology implementation.
The Experiment:
This unique experiment took place in Russia, led by a young Russian management team from the Russian Academy of National Economy and Public Administration RANEPA. Despite years of efforts to implement Japanese Lean Manufacturing at a manufacturing enterprise, he found the results unsatisfactory. In 2007, during a visit to the Applied Research Centre of ISEE with colleagues, he encountered the second version of ISEE’s Business Digital Twin and was captivated by the theoretical underpinnings of the BMO.
The Russian management team’s interest led them to delve deeply into BMO’s theoretical framework, with two month-long visits to ISEE in the summers of 2008 and 2009. By the end of their second visit, they decided to attempt to apply the BMO practically. After securing a trust management agreement with a mid-sized Russian enterprise producing car batteries, the team took over its management from 2010 to 2012.
Outcome:
At the end of 2009, the plant employed 176 workers, producing 6,000 to 7,000 car batteries monthly, valued at EUR 190,000, totaling approximately EUR 2.3 million annually.
By the end of 2012, the workforce had grown to 196 employees, and production had increased to 32,000 to 34,000 car batteries monthly, valued at EUR 980,000, totaling approximately EUR 12 million annually.
This remarkable transformation resulted in a more than fourfold increase in labor productivity and an almost five and a half times increase in sales, with total investments over the three-year period amounting to less than EUR 1 million.
The experiment demonstrated the profound impact of the BMO’s theoretical foundations on leadership effectiveness, driving significant productivity and sales growth with minimal investment.
Implementation site: Hydraulic Elements and Systems PLC, Yambol, Bulgaria and M+S Hydraulic PLC, Kazanlak, Bulgaria
Overview:
Between 2013 and 2015, ISEE launched an experimental initiative to evaluate the capabilities of Business Model Ontology (BMO) as a knowledge that can cultivate outstanding engineering talent. The objective was to determine whether young engineers lacking prior managerial experience but well-versed in the BMO theory can establish and efficiently manage high-tech enterprises. The chosen venture for this experiment was centered around axial piston pumps and motors manufacturing.
The Experiment:
In 2008, HES Plc., a manufacturer specializing in hydraulic cylinders and a company fully involved in testing BMO management, acquired outdated technical documentation for axial piston hydraulic motors and pumps, along with some of the necessary machinery for finishing operations, all obtained as scrap. These components had been originally purchased by socialist Bulgaria in the 1980s for USD 40 million as an attempt to kickstart a new high-tech production of axial piston hydraulic motors and pumps, a venture in which socialist Bulgaria invested a huge amount of effort. However, following the collapse of the political regime in 1989, the project was abandoned without reaching a functional prototype. By the time of the acquisition of the components by HES Plc., the equipment and the documentation were obsolete. Therefore, the experiment aimed to demonstrate that the Business Model Ontology, developed by the Institute for Systemic Economic Engineering, along with its accompanying Business Digital Twins software, which is based on it, could be used as a foundation for the creation of higher-quality human capital capable of building, managing, and developing high-tech industrial enterprises or reengineer existing ones.
Three engineers aged 20, 23, and 28, with no prior enterprise management or even team management experience, were tasked to create a business for the high-tech products axial piston hydraulic motors and pumps. This involved modernizing the technical and constructive documentation, planning a whole new factory, engineering all internal processes, establishing the factory, creating work, and ultimately producing a working prototype.
It should be noted that until that moment HES plc, was accustomed to 0.01mm tolerances in its hydraulic cylinder production, which meant that the engineers were faced with the challenge of adapting to the tighter 0.001mm tolerances required for piston motors and pumps. This endeavor represented a significant leap into high-tech territory for the company, and was given to a young team with no prior management experience but with deep Business Model Ontology understanding.
Outcome:
Within two years, the team of three engineers successfully planned and designed the production process and the factory layout, created engineering drawings and developed training materials for workers, created the factory, and trained six new workers. Their effort culminated in the creation of a working prototype. The produced prototype was sent to a German test laboratory, where it outperformed and gave better results than the competitive models of Bosch Rexroth. Remarkably, the team of three engineers achieved this with a minimal investment of 0.75 million USD, contrasting starkly with Bulgaria’s previous multimillion dollar and multi-year attempt that involved a team of one hundred individuals. Furthermore, when inquiries were sent to foreign experts in the field, they quoted nearly 1 million USD to update the technical and constructive documentation, which highlights the success and cost-effectiveness of enterprise creation when engineers implement the BMO principles.
Implementation site: Hydraulic Elements and Systems PLC, Bulgaria.
Overview:
In 2021, Unitraf JSC, a manufacturer of transformers, reactors, machined parts, and components, embarked on a transformative, organizational reengineering journey by implementing the Business Model Ontology (BMO) within their management practices. This initiative aimed to completely remodel the organizational culture in line with BMO theory, aiming to achieve significant advancements across the enterprise.
The Experiment:
The implementation was initiated by the owners of Unitraf JSC within their dry-type electrical transformer and metalworking enterprise comprising 50 employees. A new management team, appointed without prior experience in enterprise management, led the transformation. The focus was on adopting the BMO principles as the enterprise’s organizational culture with the aim of enhancing the organizational structure, optimizing processes, and fostering a culture of continuous and sustainable improvement.
Outcome:
The results of the BMO implementation were as follows:
- Profit Surge: The enterprise saw a 357% surge in profit, underscoring the financial success driven by the new management practices.
- Revenue Growth: Within one year, Unitraf JSC experienced a 50% increase in revenue.
- Value Addition: There was a significant 127% increase in added value, reflecting enhanced operational efficiency and product quality over the three divisions of the enterprise – transformers, manufacturing, electronics.
- Product Diversification: The company ventured into electronic equipment manufacturing, including UPS devices and sales of Solar Hybrid Inverter solutions, further diversifying its product portfolio.
- Employee Compensation: The average salary of employees increased by 50%, showcasing the positive impact on workforce motivation and retention.
- Infrastructure Expansion: A new manufacturing hall was constructed, and the shop floors of both the transformer manufacturing and metalworking operations were expanded.
The implementation of BMO at Unitraf JSC demonstrated the transformative impact of strategic, theory-based organizational management on SMEs. By remodeling the organizational culture and optimizing management practices, Unitraf JSC not only achieved substantial financial and operational improvements but also laid the foundation for sustained growth and innovation in the manufacturing sector. This case exemplifies how SMEs can leverage BMO to achieve industrial excellence and competitive advantage in their respective markets.
Implementation site: Unitraf JSC, Bulgaria.
Overview:
Hydraulic Elements and Systems PLC (HES) is the primary laboratory-enterprise within the Applied Research Base of ISEE. Before the democratic changes of late 1989, HES operated with over 2,500 employees across four manufacturing sites. At that time, the company held over 20% of the global market for hydraulic cylinders used in electric and motor forklifts. However, by March 1997, HES was near bankruptcy, with only around 1,000 employees and an average salary of less than $10 a month. The technical environment was in a deplorable state.
The Experiment:
In March 1997, Peter Bachvarov, a co-author of the Business Model Ontology (BMO), was elected CEO at HES. This marked the beginning of a transformative journey for the company, focusing on implementing the BMO and developing the Business Digital Twin software.
- 1997-2001: Initial Phase
Recruitment and Training: HES hired 12 young machine engineers with minimal professional experience in 1997. By mid-1998, these engineers were introduced to the initial form of the holistic BMO.
Development of BDT: An initial variant of the 1st version of ISEE’s Business Digital Twin was provided to these engineers, enabling digitalization of engineering developments to manage sales, production, and supply systems. The first version of the BDT was completed by the end of 2001.
- 2002-2003: First Campaign for Large-Scale Industrial Reengineering
Restructuring and Relocation: Over 80% of all workplaces were restructured and relocated within 15 months, managed by those young engineers using the Business Digital Twin software.
Focus on Engineering Developments: The engineering developments included labor norms, material limits, and “engineering organizational cost analyses” of products, all embedded in the Business Digital Twin.
- 2010-2011: Second Campaign for Large-Scale Industrial Reengineering
Economic Crisis Response: Following the global economic crisis, a second reengineering campaign was launched, utilizing the 3rd version of the BDT system.
Continued Improvement: This campaign saw over 70% of workplaces restructured and relocated, resulting in a more than twofold increase in production volume and diversity.
Outcome:
The results of the two campaigns demonstrated a profound transformation at HES.
Technical Environment Transformation:
The state of the technical environment improved significantly from 1997 to 2011, with modernized equipment and processes. Before the implementation of BMO, the technical environment was outdated and inefficient, but by 2011, it had been transformed into a state-of-the-art facility. This included upgraded machinery and streamlined production lines, which greatly enhanced operational efficiency.
Economic Growth:
Sales increased substantially over the twenty-year period, despite the global economic crisis of 2008/2009. The holistic ERP system enabled better resource management, cost control, and market responsiveness, which resulted in a steady increase in revenue. Even during economic downturns, HES managed to maintain growth by optimizing its production processes and expanding its market reach.
Batch Size Reduction:
The ability to engineer and manufacture products in small batches improved dramatically, enhancing flexibility and efficiency. Initially, HES operated with large batch sizes, which limited its ability to respond to market changes. By implementing the holistic ERP system, the company was able to reduce batch sizes, allowing for more customized production runs and quicker turnaround times.
New Product Implementation:
The capability to introduce new products saw significant growth, from no new product engineering developments in 1997 to a robust system by 2011. The holistic BMO framework facilitated innovation by integrating product development with production and supply chain management. This seamless integration allowed HES to rapidly develop and launch new products, meeting evolving customer demands.
Organizational Shift:
The role of engineers evolved from servicing in 1997 to central management by 2003, reflecting a shift towards a knowledge-driven organization. The transformation involved not only technological advancements but also a cultural shift within the organization. Engineers became central to the decision-making process, leveraging their expertise to drive strategic initiatives and continuous improvement
The transformative journey of HES, powered by the holistic BMO and a holistic ERP system, highlights substantial improvements in the technical environment, economic performance, and organizational structure. This case study underscores the efficacy of BMO in driving large-scale industrial reengineering and achieving sustainable growth. The success of HES demonstrates that with the right strategic approach and technological integration, even enterprises on the brink of failure can achieve remarkable turnaround and long-term prosperity
Implementation site: Hydraulic Elements and Systems PLC, Yambol, Bulgaria.
Overview:
ISEE has executed numerous industrial reengineering campaigns, with two major initiatives reshaping over 500 workplaces. The first of these large-scale efforts demonstrated the transformative power of the second version of the Business Digital Twin (BDT) system.
First Campaign: 2002-2003
The Experiment:
The initial large-scale reengineering campaign was conducted over approximately 15 months, between 2002 and 2003, utilizing the second version of the BDT system. During this period, over 80% of all workplaces were restructured and relocated. Remarkably, the project was managed by several young engineers, each with less than three years of professional experience but highly proficient in using the BDT system for modeling technological environments and industrial processes.
Outcome:
The campaign was executed swiftly and efficiently without any interruption to industrial processes. In fact, production volume and diversity increased during the reengineering process. The success of this campaign highlighted the effectiveness of the second version of the BDT system in managing and executing large-scale industrial transformations with minimal disruption.
Second Campaign: 2010-2011
The Experiment:
Following the global economic crisis, ISEE embarked on a second large-scale industrial reengineering campaign from the spring of 2010 to the summer of 2011, utilizing the third version of the BDT system. During this period, more than 70% of all workplaces were restructured and relocated. This initiative was undertaken amidst challenging economic conditions, underscoring the resilience and adaptability of the BDT system.
Outcome:
Despite the economic downturn, the reengineering campaign proceeded without delays or suspension of industrial activities. Production not only continued but accelerated, with a more than twofold increase in both volume and nomenclature. The campaign’s success was unprecedented, with ISEE’s studies indicating no comparable industrial reengineering effort in terms of investment efficiency and performance, achieved largely due to the advanced capabilities of the third version of the BDT system.
Conclusion:
These two campaigns collectively demonstrate the BDT system’s unparalleled effectiveness in facilitating large-scale industrial reengineering, even under challenging circumstances. The evolution from the second to the third version of the BDT system showcased significant advancements in technology and methodology, enabling remarkable improvements in productivity and operational efficiency.
Implementation site: Hydraulic Elements and Systems PLC, Yambol, Bulgaria.
Overview:
In 2005, ISEE embarked on a project to assess the capabilities of the Business Digital Twin (BDT) software as a system for quality management and as an enabler for a seamless ISO 9001:2000 certification process.
The Experiment:
To thoroughly evaluate the BDT software, ISEE collaborated with two globally renowned certification bodies – Lloyd’s Register and TÜV Rheinland. The project team from ISEE included one engineer proficient in the BDT software and an assistant. The consultants from Lloyd’s Register and TÜV Rheinland initially anticipated that implementing the necessary documents for quality management procedures would take several months, typically around 4 to 6 months, followed by an extended period for the actual certification audit, which usually takes an additional 3 to 6 months. Therefore, they expected the total process to take between 7 to 12 months.
However, upon familiarizing themselves with the BDT software, the consultants discovered that all necessary forms and information were already integrated into the system. The only task remaining was to format the information provided by the Business Digital Twin according to the standards recognized by the certification bodies.
Outcome:
Remarkably, by mid-December 2005, less than two months after the project commenced, Lloyd’s Register and TÜV Rheinland issued the ISO 9001:2000 certification to Hydraulic Elements and Systems PLC. Over the following years, TÜV Rheinland frequently used ISEE’s implementation as a model of “good practices” for other companies seeking ISO 9001:2000 certification, showcasing the effectiveness and efficiency of the BDT software.
Implementation site: Hydraulic Elements and Systems PLC, Yambol, Bulgaria.
Overview:
In 2009, ISEE undertook a project to demonstrate the capabilities of the Business Digital Twin (BDT) software in implementing Single-Minute Exchange of Die (SMED) and lean manufacturing principles.
The Experiment:
Between 2009 and 2010, over the course of 18 months, two engineers with no prior experience in plant design or lean manufacturing theory, but highly proficient in the ISEE Business Digital Twin BDT system and its cognitive platforms, developed and implemented a system for SMED and lean manufacturing. This system was deployed across two technological fields, encompassing a total of approximately 40 digital programming operational places.
Outcome:
The implementation of SMED resulted in a remarkable increase in productivity, with the 40 operational places in question experiencing a 5 to 10-fold productivity improvement. This was achieved with minimal costs. Additionally, a comprehensive personnel training program was developed to ensure the sustainability of these improvements.
In comparison, developing and rolling out such a system on a global scale within a plant owned by a large Western company would typically take around 6 years, requiring significantly greater human and financial resources. This stark contrast highlights the efficiency and effectiveness of the BDT software in facilitating lean manufacturing practices.
Implementation site: Battery plant Tungstone, Ryazan, Russia
Overview:
In 2010, ISEE initiated a groundbreaking project to assess the Business Model Ontology (BMO) as a tool for educating highly effective leaders, diverging from previous experiments by focusing on theoretical foundations rather than direct digital technology implementation.
The Experiment:
This unique experiment took place in Russia, led by a young Russian management team from the Russian Academy of National Economy and Public Administration RANEPA. Despite years of efforts to implement Japanese Lean Manufacturing at a manufacturing enterprise, he found the results unsatisfactory. In 2007, during a visit to the Applied Research Centre of ISEE with colleagues, he encountered the second version of ISEE’s Business Digital Twin and was captivated by the theoretical underpinnings of the BMO.
The Russian management team’s interest led them to delve deeply into BMO’s theoretical framework, with two month-long visits to ISEE in the summers of 2008 and 2009. By the end of their second visit, they decided to attempt to apply the BMO practically. After securing a trust management agreement with a mid-sized Russian enterprise producing car batteries, the team took over its management from 2010 to 2012.
Outcome:
At the end of 2009, the plant employed 176 workers, producing 6,000 to 7,000 car batteries monthly, valued at EUR 190,000, totaling approximately EUR 2.3 million annually.
By the end of 2012, the workforce had grown to 196 employees, and production had increased to 32,000 to 34,000 car batteries monthly, valued at EUR 980,000, totaling approximately EUR 12 million annually.
This remarkable transformation resulted in a more than fourfold increase in labor productivity and an almost five and a half times increase in sales, with total investments over the three-year period amounting to less than EUR 1 million.
The experiment demonstrated the profound impact of the BMO’s theoretical foundations on leadership effectiveness, driving significant productivity and sales growth with minimal investment.
Implementation site: Hydraulic Elements and Systems PLC, Yambol, Bulgaria and M+S Hydraulic PLC, Kazanlak, Bulgaria
Overview:
Between 2013 and 2015, ISEE launched an experimental initiative to evaluate the capabilities of Business Model Ontology (BMO) as a knowledge that can cultivate outstanding engineering talent. The objective was to determine whether young engineers lacking prior managerial experience but well-versed in the BMO theory can establish and efficiently manage high-tech enterprises. The chosen venture for this experiment was centered around axial piston pumps and motors manufacturing.
The Experiment:
In 2008, HES Plc., a manufacturer specializing in hydraulic cylinders and a company fully involved in testing BMO management, acquired outdated technical documentation for axial piston hydraulic motors and pumps, along with some of the necessary machinery for finishing operations, all obtained as scrap. These components had been originally purchased by socialist Bulgaria in the 1980s for USD 40 million as an attempt to kickstart a new high-tech production of axial piston hydraulic motors and pumps, a venture in which socialist Bulgaria invested a huge amount of effort. However, following the collapse of the political regime in 1989, the project was abandoned without reaching a functional prototype. By the time of the acquisition of the components by HES Plc., the equipment and the documentation were obsolete. Therefore, the experiment aimed to demonstrate that the Business Model Ontology, developed by the Institute for Systemic Economic Engineering, along with its accompanying Business Digital Twins software, which is based on it, could be used as a foundation for the creation of higher-quality human capital capable of building, managing, and developing high-tech industrial enterprises or reengineer existing ones.
Three engineers aged 20, 23, and 28, with no prior enterprise management or even team management experience, were tasked to create a business for the high-tech products axial piston hydraulic motors and pumps. This involved modernizing the technical and constructive documentation, planning a whole new factory, engineering all internal processes, establishing the factory, creating work, and ultimately producing a working prototype.
It should be noted that until that moment HES plc, was accustomed to 0.01mm tolerances in its hydraulic cylinder production, which meant that the engineers were faced with the challenge of adapting to the tighter 0.001mm tolerances required for piston motors and pumps. This endeavor represented a significant leap into high-tech territory for the company, and was given to a young team with no prior management experience but with deep Business Model Ontology understanding.
Outcome:
Within two years, the team of three engineers successfully planned and designed the production process and the factory layout, created engineering drawings and developed training materials for workers, created the factory, and trained six new workers. Their effort culminated in the creation of a working prototype. The produced prototype was sent to a German test laboratory, where it outperformed and gave better results than the competitive models of Bosch Rexroth. Remarkably, the team of three engineers achieved this with a minimal investment of 0.75 million USD, contrasting starkly with Bulgaria’s previous multimillion dollar and multi-year attempt that involved a team of one hundred individuals. Furthermore, when inquiries were sent to foreign experts in the field, they quoted nearly 1 million USD to update the technical and constructive documentation, which highlights the success and cost-effectiveness of enterprise creation when engineers implement the BMO principles.
Results following the implementation of Business Digital Twin
Results following the implementation of Business Digital Twin
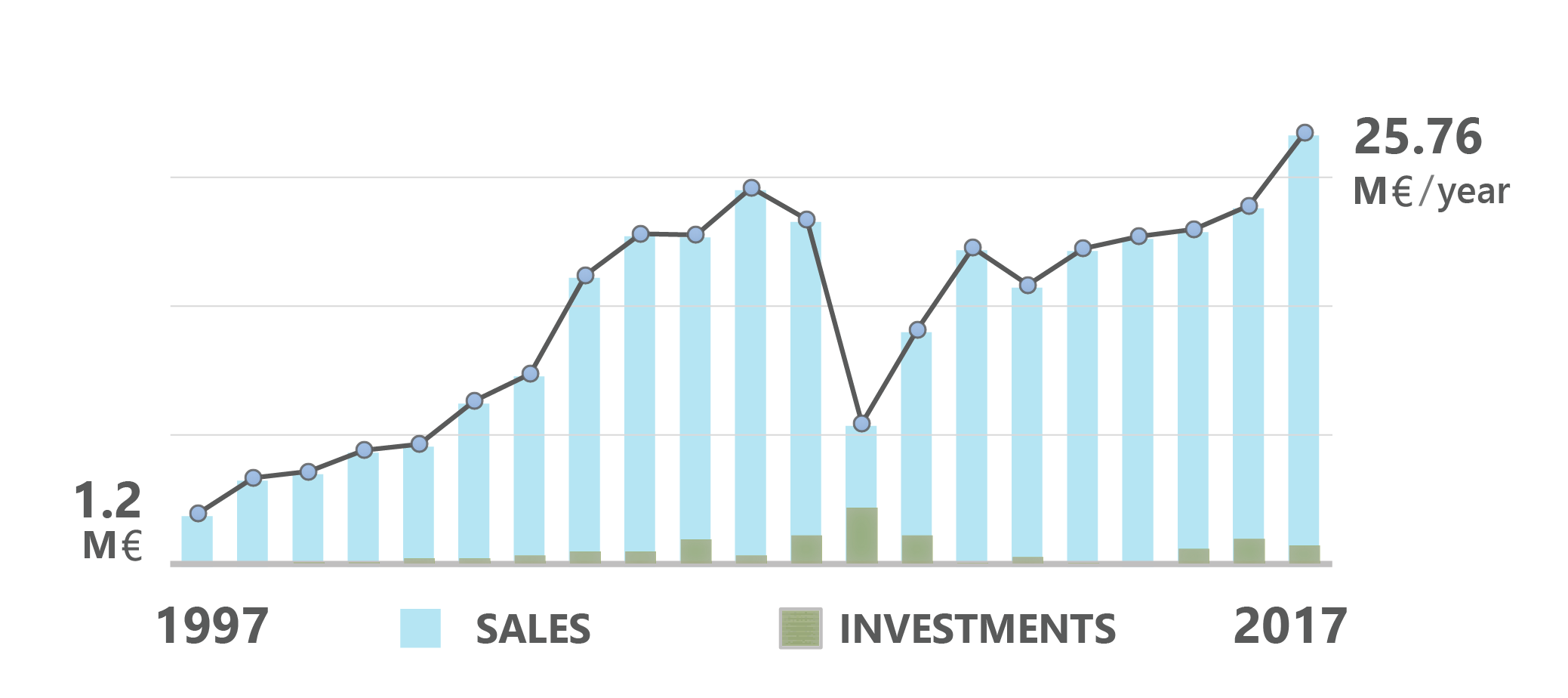
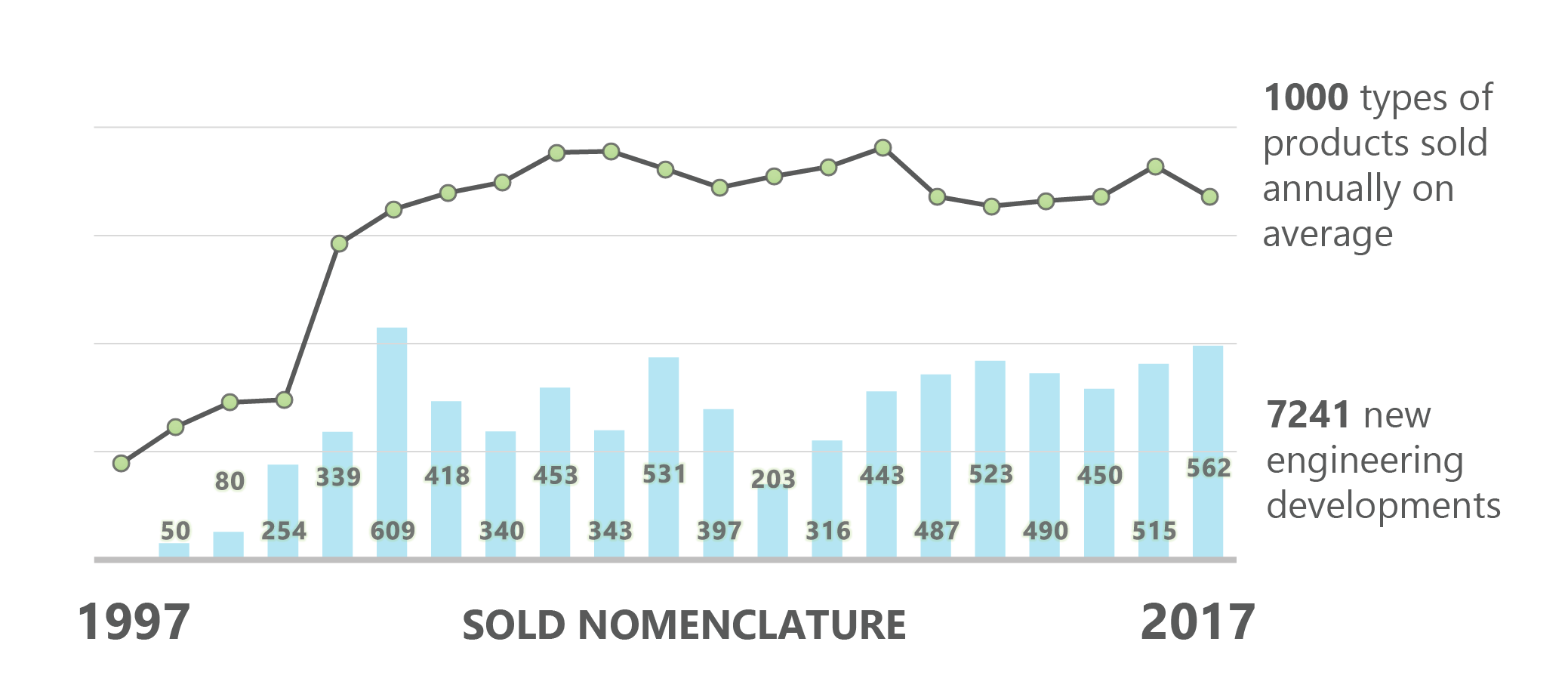
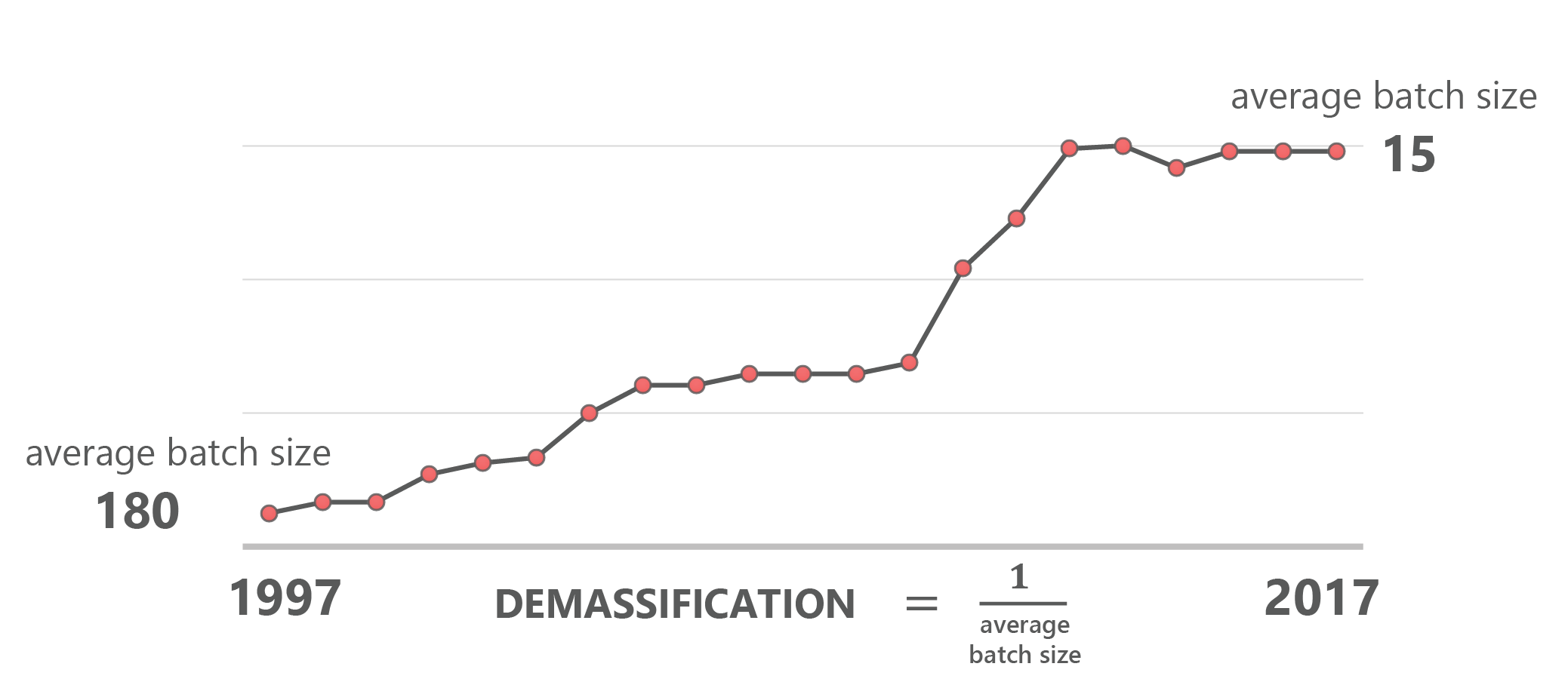
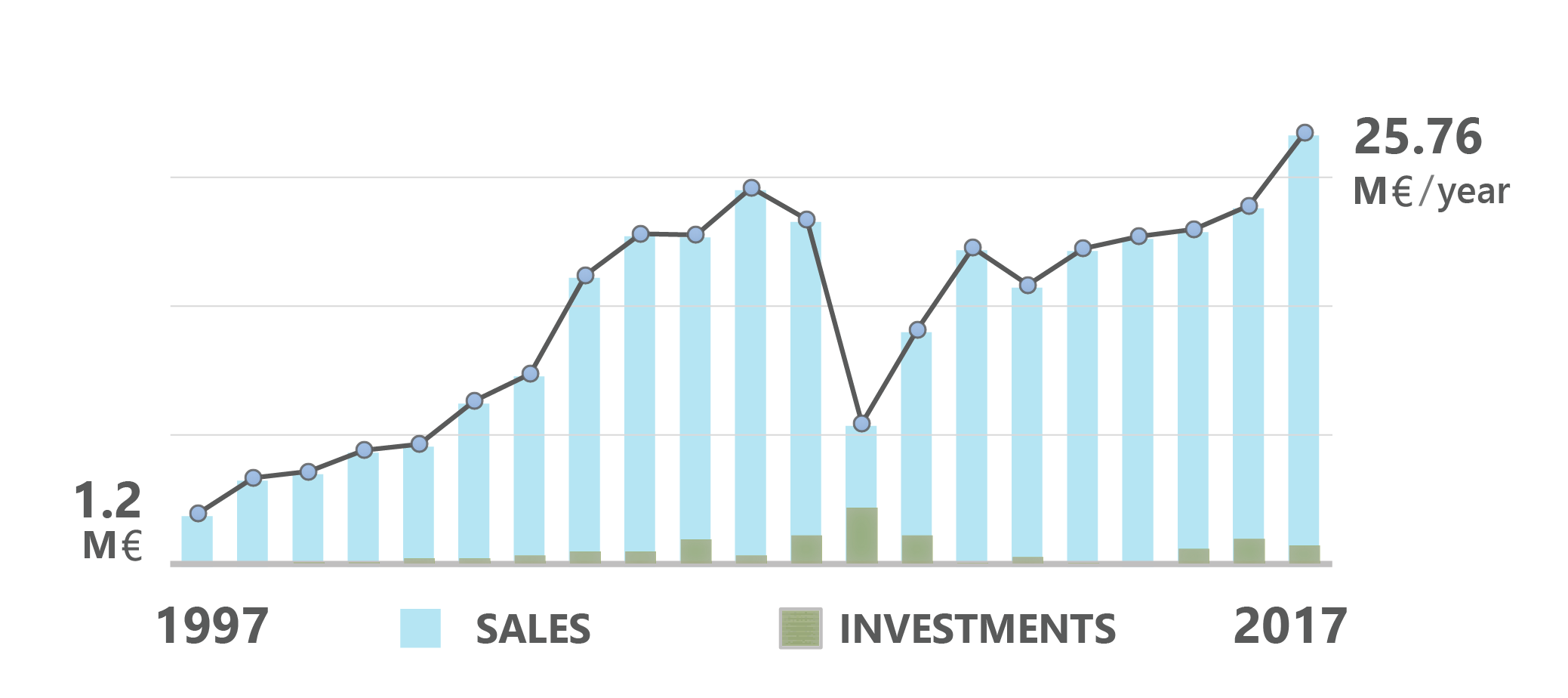
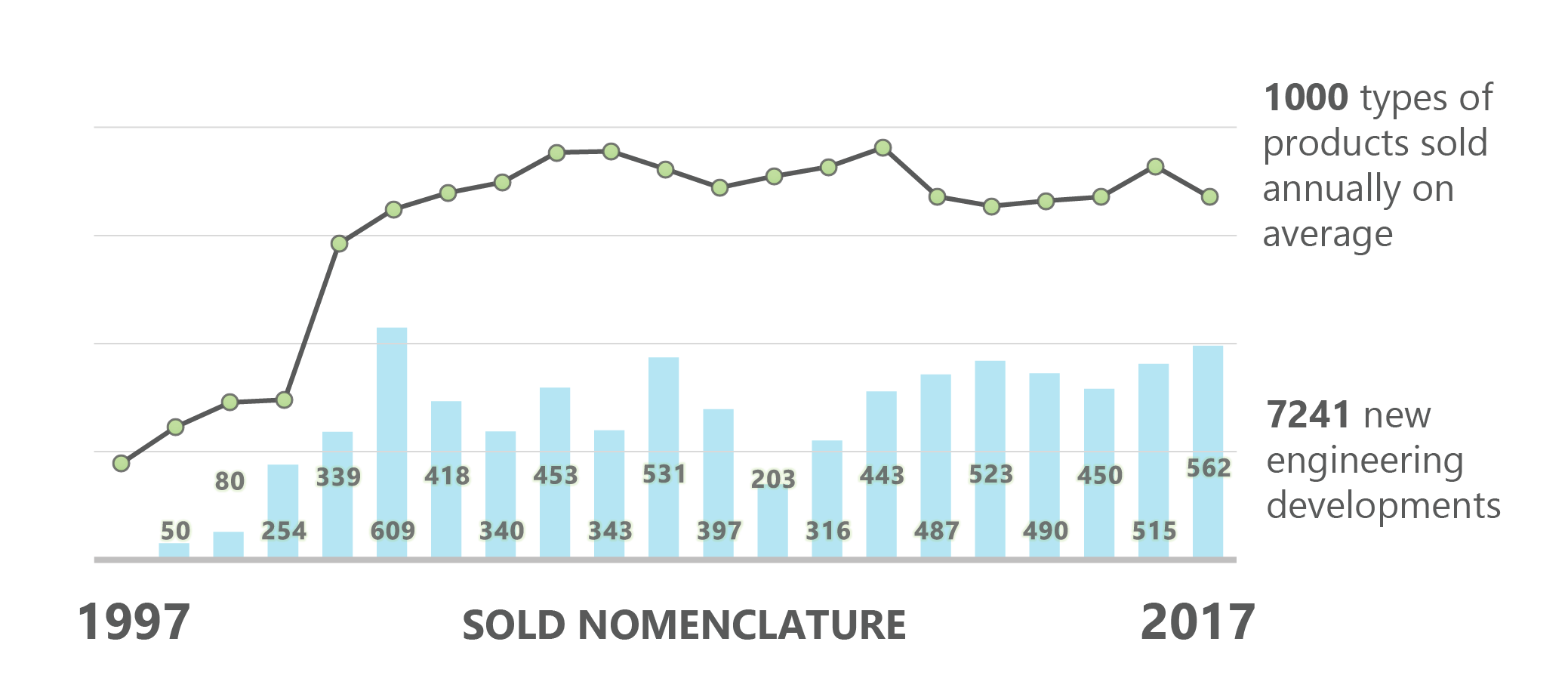
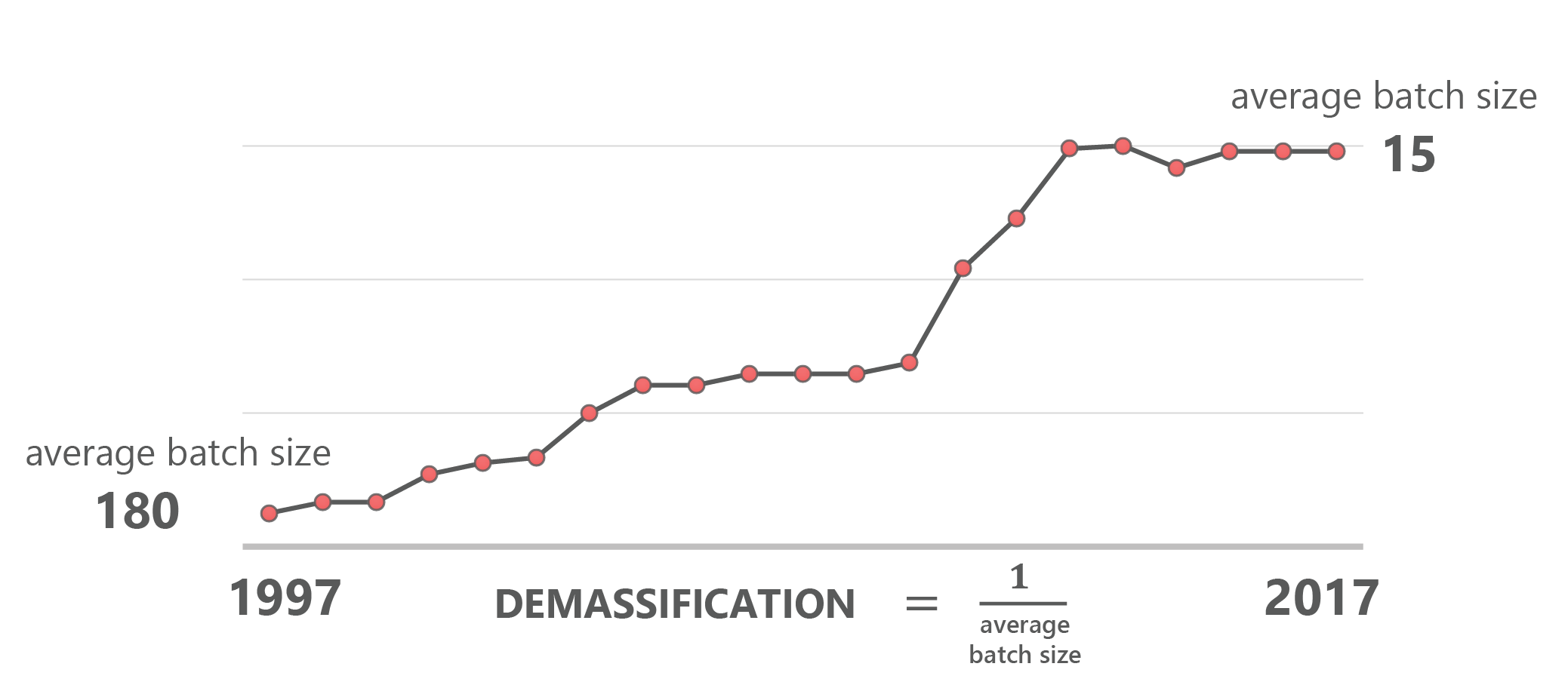